Gelişen teknoloji sayesinde sağlık alanında pek çok yenilik özel uygulamaları da beraberinde getirmekte. Sağlık alanındaki son yılların en aktif ve üretken konusu hiç şüphesiz kök hücre tabanlı tedavi hizmetleridir. Gerek karmaşık yapısı gerekse elde etme, üretme, saklama ve uygulama açısından sayısız özel duruma sahip olması nedeniyle kök hücre çalışmaları da özel kontrollü alanlara ihtiyaç duymaktadır. Klasik ilaç üretim tesislerinde olduğu gibi temiz odaların yanı sıra, kök hücre üretim ve uygulamalarında pek çok laboratuvar ekipmanı da sürece dahil olmaktadır. Görece yeni kabul edilen ve ülkemizde de her geçen gün önemi artan bu alanda regülasyona uygunluk, verim ve kalite açısından üretim alanlarının izlenilmesi gerekmektedir. Bu izleme sistemleri hakkında sıkça karşılaştığımız soru ve cevapları sizlerle paylaşmak isterim.
1. Kök Hücre Laboratuvarlarında izlenilmesi gereken ekipman ve izleme parametreleri nelerdir?
Üretim sürecine doğrudan dahil olan ve canlı hücrelerin işlenildiği iş akış sürecindeki tüm ürün ve ekipmanlar izleme sistemine dahil edilmelidir. Burada laboratuvardaki iş akışının A’dan Z’ye ele alınması gerekmektedir. Örneğin, ilk etapta üretim sürecine doğrudan dahil olan GMP Grade B temiz odaların açıldıkları koridora olan fark basınçlarından başlayıp, ortam hava sıcaklığı ve bağıl neminin üretime uygun olması, çalışmanın yapılacağı ve hücrelerin doğrudan atmosfere açık olacağı GMP Grade A biyogüvenlik kabini (BSC) ve laminar hava akış kabinlerinde (LAF) partikül seviyesinin izlenilmesi gibi sürece dahil olan tüm ortam koşulları ve ekipmanlar buna dahil edilmelidir.
Genel bir Kök Hücre Laboratuvarında izlemeye dahil edilen ekipmanlar ve izlenen parametreler tablosu şu şekildedir;
|
Sıcaklık
|
Bağıl Nem
|
Fark Basınç
|
Partikül
|
Oksijen
|
Karbondioksit
|
GMP Grade C/B Üretim Hava Kilidi (Airlock)
|
√
|
√
|
√
|
|
|
|
GMP Grade B Üretim Koridoru
|
√
|
√
|
√
|
|
|
|
GMP Grade B Üretim Oda
|
√
|
√
|
√
|
√
|
|
|
BSC (Grade A)
|
|
|
|
√
|
|
|
LAF Kabini (Grade A)
|
|
|
|
√
|
|
|
Inkübatör
|
√
|
|
|
|
√
|
√
|
Etüv
|
√
|
|
|
|
|
|
Buzdolabı
|
√
|
|
|
|
|
|
Derin Dondurucu
|
√
|
|
|
|
|
|
Ultra Derin Dondurucu
|
√
|
|
|
|
|
|
Kriyojenik Tank
|
√
|
|
|
|
|
|
Karantina Odası
|
√
|
√
|
√
|
|
|
|
Kalite Kontrol Odası
|
√
|
√
|
|
|
|
|
Tablo 1 - İzlemeye Dahil Edilen Ekipmanlar ve İzlenen Parametreler
Burada dikkat edilmesi gereken birkaç hususu listeleyelim;
- Üretime doğrudan dahil olmayan, test ve/veya kontrol amaçlı LAF kabinlerinin online izleme sistemine dahil edilmesi gerekmemektedir. GMP’ye uygun bir izleme sisteminin amacı doğrudan üretilen ürünü ve ürünle doğrudan temas halinde olan ortamları izlemektir. Aynı koşul diğer laboratuvar ekipmanları için de geçerlidir.
-
- Sahanın kendine özgü şartları göz önüne alınarak yerinde risk değerlendirmesi yapılmalıdır. Örneğin, aktif olarak kullanılan ve numunenin işlendiği/paketlendiği veya test edildiği B sınıfı bir koridor aktif bir oda gibi değerlendirilmeli ve oda içerisinde de partikül izlemesi yapılmalıdır. Benzer şekilde, temiz odanın aktif kullanılan steril odalarının tamamında fark basınç izlemesi yapılması riski azaltmaya yardımcı olacaktır.
-
- Sensör yerleşiminde cihazların boyutları, bağımsız ve farklı amaçlarla kullanılan bölmeleri göz önüne alınarak birden fazla sensör kullanılabilir.
-
- Temiz odalar, operatör odası ve kriyojenik tankların yer aldığı alanlarda operatörleri doğrudan sesli ve görsel olarak ikaz edecek alarm kuleleri yer almalıdır. Bu alarm kuleleri; yeşil, sarı ve kırmızı gibi normal durum, alarm durumu ve aksiyon durumunu ayrı ayrı belirtecek şekilde kodlanmalıdır.
-
- Sahanın kullanımda olmadığı ve operatörün sahada olmadığı durumlarda, numuneleri ve ürünleri koruma amaçlı alarm ve ikaz parametreleri, ilgili kişilere email, SMS, sesli mesaj ve benzeri uzak ikaz metotları ile iletilebilinir.
2. İzleme sistemlerinde uygunluğun aranması gereken standart ve regülasyonlar var mıdır?
Kök hücre izleme sistemleri GMP Ek 1 kılavuzunda belirtildiği şekilde sınıflandırılan A,B,C ve D alanlara sahiptir. Bu alanlarda 6 aylık ve 12 aylık kalifikasyon testlerinde olduğu gibi, sürekli izleme sistemleri de GMP Ek 1’de yer alan “cleanroom monitoring” başlığına uygun şekilde izlenmelidir. Bunun yanında, sistemlerin Uluslararası İlaç Mühendisliği Derneği (ISPE) tarafından yayınlanan GAMP5 (Good Automated Manufacturing Practice Vol.5) dökümanında bilgisayarlı izleme sistemleri için risk tabanlı yaklaşım tüm yönleri ile ele alınarak validasyon süreci net bir biçimde tanımlanmıştır. Ayrıca "International Conference on Harmonization (ICH)" (Uluslararası Uyumlandırma Konferansı) olarak bilinen bir süreçte yayınlanan ICHQ9 “Kalite Risk Yönetimi” dökümanı da özellikle kurulum öncesi ve sonrası risk değerlendirmelerinde yardımcı olmaktadır.
3. Bina İzleme Sistemimiz var, harici bir sisteme yine de ihtiyacımız var mı?
Laboratuvar sürekli izleme sistemlerinde belki de en sık karşılaşılan soru, halihazırda Bina Yönetim Sistemi/Bina Otomasyonu (BMS) tarafından toplanan verilerin Çevresel İzleme Sistemi verileri olarak kalite açısından da kullanılıp kullanılamayacağıdır. Öncelikle BMS sistemleri, iklimlendirme sisteminin düzenli kontrolü açısından veri toplayan ve amacı ısıtma, soğutma ve iklimlendirme (HVAC) sistemini kumanda etmek olan bir otomasyondur.
Tablo 2’de yer alan karşılaştırma BMS ile Çevresel İzleme Sistemi’nin net bir şekilde birbirinden ayrıldığını göstermektedir.
|
Bina Otomasyonu (BMS)
|
Çevresel İzleme Sistemi
|
Amaç
|
Temel amaç bina iklimlendirme sistemi, yangın algılama sistemi ve güvenlik sistemini kontrol etmektir.
|
Üretim sürecinde olası her türlü limit dışı durumu anında tespit etmek ve operatörü ikaz etmektir.
|
Sensör Konumu
|
Çevresel veriler için sensor noktaları hava dönüşleri, menfezler ve servis alanlarıdır.
|
Sahada sensör noktaları risk tabanlı bir yaklaşımla, gerekli hallerde termal haritalandırma ve en kötü durum senaryosu ile seçilir.
|
İkaz ve Kontrol
|
Veriler operatörlerle iletişim amaçlı değil HVAC ve diğer sistemler için kontrol parametresi oluşturma amaçlı toplanır.
|
Sahadaki olası herhangi bir ikaz doğrudan operatörlere sesli, görsel şekilde alarm kuleleri vasıtasıyla iletilir. Sistemin kontrol etme gibi bir görevi yoktur. Amaç veriyi sağlıklı biçimde toplayıp yorumlamak ve olası sapmaları tespit etmektir.
|
Validasyon
|
Gerekli değildir. Data doğruluğu ve sürekliliği birinci derece öncelikli değildir.
|
Sistemin valide edilmesi ve her türlü hata, arıza ve data kaybı senaryolarının Dizayn Kalifikasyonunda irdelenmiş olması ve IQ ve OQ fazında test edilmiş olması esastır.
|
Kalibrasyon
|
Sensörler genellikle çalıştıkları süre içerisinde düzenli kalibrasyona tabi tutulmazlar.
|
Sensörler 6 ay/12 ay aralığında en az 1 kez kalibre edilmektedir.
|
Tablo 2 - Bina Otomasyon Sistemi ve Çevresel İzleme Sistemi Arasındaki Farklar
4. Kullandığımız ekipmanlar halihazırda gereken tüm parametreleri ölçüp kontrol edebiliyor, sistemi bu altyapıda izleyebilir miyiz?
Bina otomasyon sistemine benzer şekilde laboratuvarda kullanılan Etüv, İnkübatör, Buzdolabı, Derin Dondurucu ve Kriyojenik Tanklar gibi ekipmanlar dahili arayüzlerinde bahse konu olan dataları verebilmekte, istenildiği taktirde bu verileri bir arayüz sayesinde merkezi bir yazılıma da aktarabilmektedir. Ancak, GMP uyumlu çevresel izleme sistemleri, tıpkı bir bekçi gibi bu cihazların olası sensör arızalarını ve cihazı kumanda eden verileri de izlediğinden dolayı ikinci bir güvenlik seviyesi oluşturmaktadır. Benzer şekilde GMP uyumlu çevresel izleme sisteminde bir arıza olması durumunda da bu kez cihazın dahili sensörü sayesinde sürece müdahale etmek ve olası hata ve kayıpların önüne geçmek mümkün olacaktır.
5. Tüm kritik veriyi toplamak için datalogger (veri toplayıcı) kullanıyoruz. Yeterli midir?
Veri toplayıcılar, cihazların trendini belirleme, alarm ve aksiyon limitlerinin tespit edilebilmesinde anahtar rol oynayabilir. Ancak GMP uyumlu çevresel izleme sistemlerinin yerini tutamazlar. Çünkü olası bir alarm durumunda bu alarmdan haberdar olabilmeniz için veri toplayıcı üzerindeki datanın bilgisayara aktarılması gerekmektedir. Bu da alarm koşulundan operatörlerin müdahale edebilecekleri süre geçtikten sonra haberdar olmaları anlamına gelmektedir. Genellikle veri toplama cihazlarını ısı haritalandırma, en kötü durum senaryosu ve trend izleme amaçlı olarak kullanmaktayız. GMP uyumlu çevresel izleme sistemlerinde ise amaç, olası alarm durumunda operatörü en hızlı ve en etkin şekilde haberdar etmektir.
6. Bina Otomasyon Sistemi (BMS) sensörlerinden alınan verilerle GMP Uyumlu Çevresel İzleme Sistemi verileri farklılık gösterebilir mi?
BMS sistemlerinde sensör yerleşimi HVAC sisteminin en verimli şekilde çalışmasına yetecek veriyi toplama amaçlı yapılmaktadır. Bu nedenle, örneğin sıcaklık verisi, dönüş havalarından ve/veya odaya sağlanan temiz hava kanallarından alınmaktadır. Bu durumda, risk tabanlı yaklaşımla oda içerisinde seçilen nokta ile BMS için seçilen noktada ölçülen değerler farklılık gösterebilmektedir. Buna sensörlerin hassasiyeti, kalibrasyon durumu ve histerisizliği de eklenerek ele alınırsa değerlerin bire bir aynı olmayabilir. GMP uyumlu izleme sistemleri GAMP5’e uygun olarak validasyonu yapıldığı için, operasyonel kalifikasyon sırasında her bir sensör yerinde referans bir sensör ile test edilmekte ve verinin doğruluğu onaylanmaktadır. Bu nedenle BMS ile Çevresel İzleme Sistemi’ndeki verilerin aynı olmasını beklememek gerekir.
7. Partikül İzleme Sistemleri 1 metreküp hava örneklemeli midir? Alarmlar m3’teki limitlere uygun şekilde mi belirlenmelidir?
Bu soruyla yalnızca Kök Hücre Laboratuvarlarındaki değil, ilaç üretim tesislerindeki partikül izleme sistemlerinde de sıkça karşılaşmaktayız. Öncelikle GMP Ek 1 kılavuzu hem temiz oda sınıflandırma (classification) hem de online izleme (monitoring) konusunda regülasyon sağlamaktadır. Dokümanın 4-7 arası tüm maddeleri “Clean room and clean air device classification” olarak verilmiştir ve sınıflandırma tablosu bu kısımda yer alır;
Tablo 3 - GMP Ek 1 Kılavuzunda Yer Alan Her Bir Sınıf İçin Partikül Limitleri
GMP Ek 1 kılavuzu 5.maddede, temiz odalarda gerçekleştirilen kalifikasyon çalışmalarında, Grade A için minimum 1m3 hava örneklenmesi gerektiği net bir biçimde belirtilmiştir. Ancak, sürekli izleme koşulunda bu durum farklıdır. Sürekli izleme yine GMP Ek 1 belgesinin 8-15 maddeleri ile belirlenen şartlarda gerçekleştirilir. Burada 5.maddede “...Grade A alanlar her türlü müdahaleyi, geçici olayları ve her türlü sistem bozukluklarını tespit ederek limit dışı alarmları tetikleyebilecek numune hacmi ve ölçüm frekansında izlenmelidir...” denilmektedir. Yine 12.maddede “Otomatik sistemler kullanılarak izleme amaçlı alınan örnek hacimleri genellikle kullanılan sistemin örnekleme oranının bir fonksiyonudur. Numune hacminin, temiz odalar ve temiz hava cihazlarının resmi sınıflandırması için kullanılanla aynı olması gerekmez.” denilmektedir. Bu nedenle gerek çalışma alanındaki operatör aktif kullanım alanı ve gerekse numune hacminin çalışmaya etkisi düşünülerek farklı numune hacimleri ile her dakika numune alınıp alarm limitleri ile kıyaslanmalı ve aşım durumlarında operatör ikaz edilmelidir.
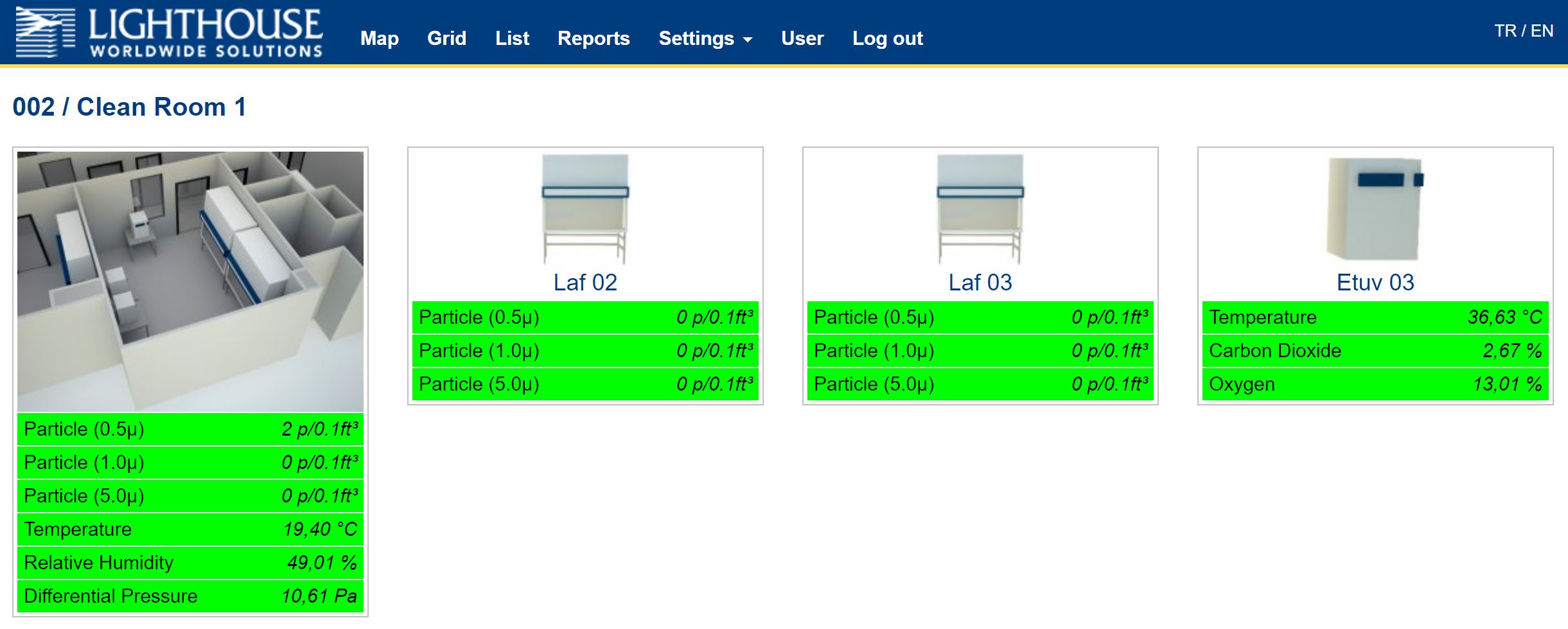